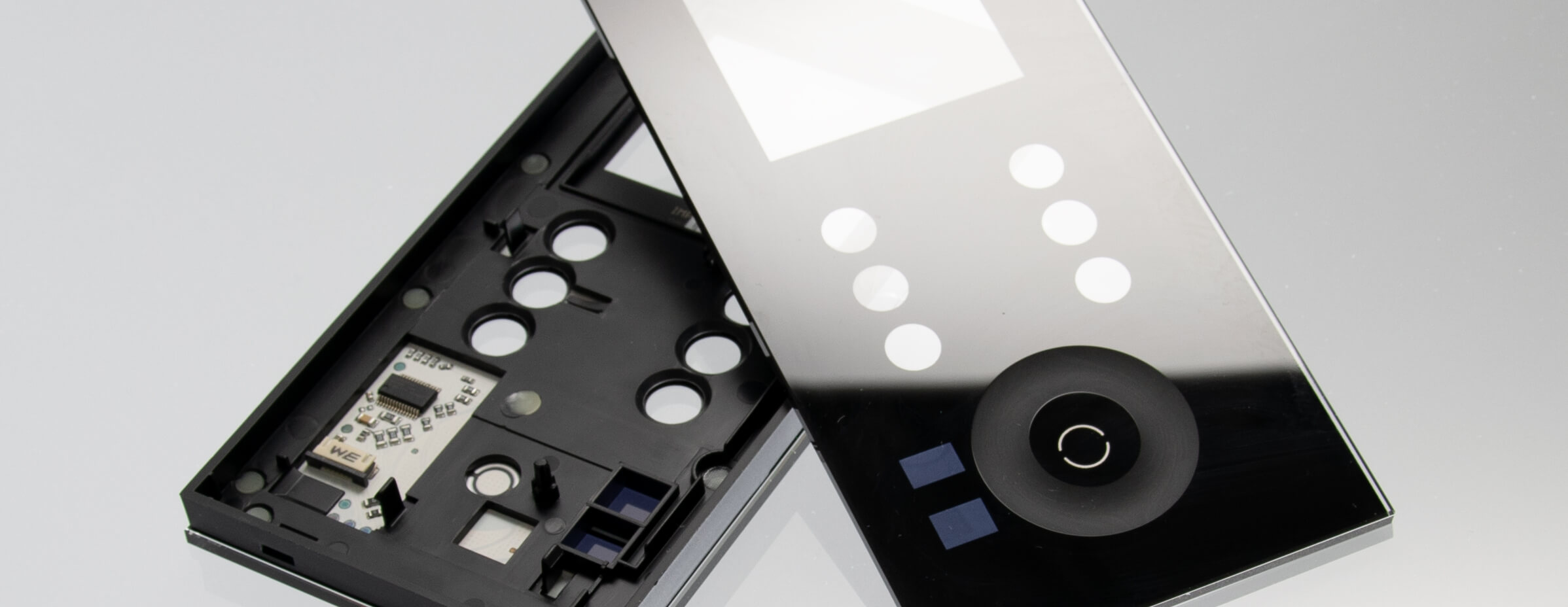
IMPAtouch®
Capacitive sensor technology printed on glass with ceramic inks. We have been printing electronic layouts directly onto glass for 20 years, offering our customers a technology platform that enables them to reduce the carbon footprint of their input systems.
Electronics on glass
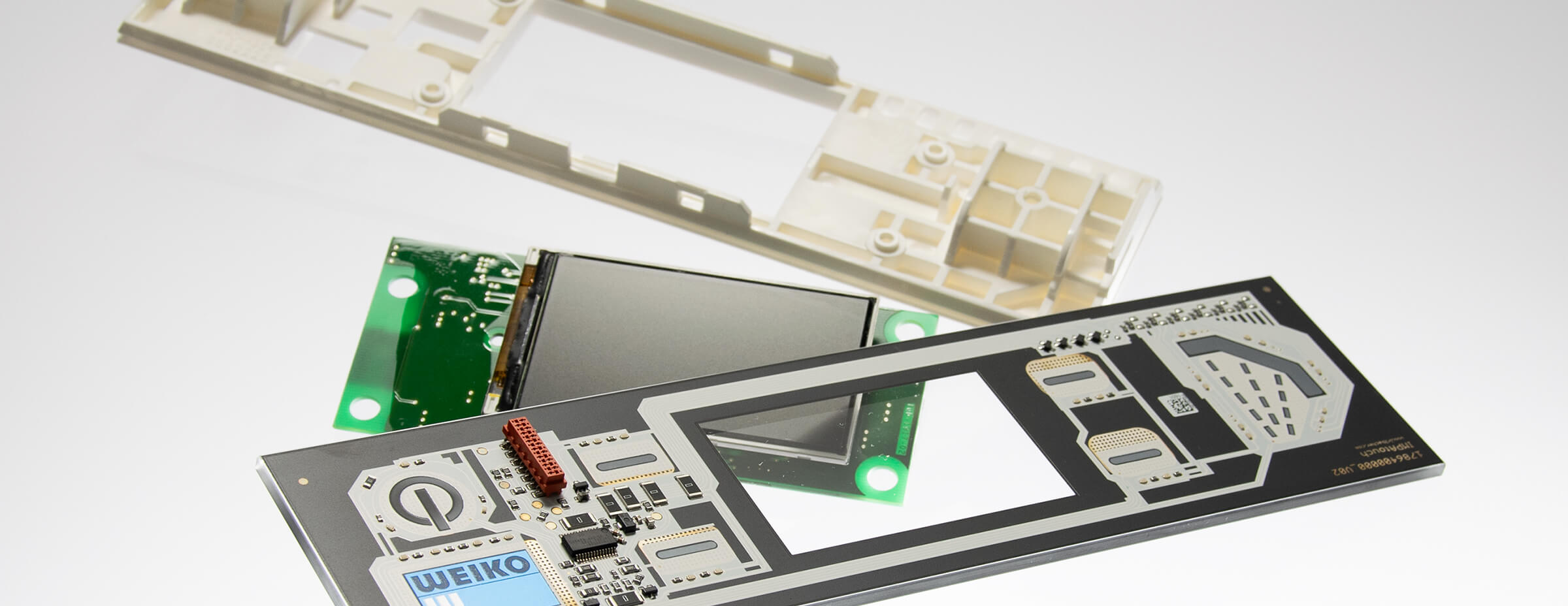
Every day, we develop new ideas, technologies and processes that give our customers a competitive advantage. For our printed electronic layouts on glass, we use inorganic, conductive coating systems to create a robust and sustainable solution for glass-based HMIs. This means that, where technically feasible, we can print circuits on glass and assemble electronic components directly on glass.
Electronic layouts printed on glass
Conductive tracks, soldering surfaces and sensors for our capacitive buttons are made of conductive ceramic paste and are screen-printed directly onto the glass under clean room conditions. The ceramic pigments fuse homogeneously with the glass during the stoving and hardening process. The result is an SMD mountable circuit board made of toughened safety glass.
Electronic components mounted on glass
The glass circuit board is fitted with all the necessary electronic components in the subsequent SMD process. The components are soldered directly onto the glass using the reflow procedure. Thanks to our IMPAtouch technology, we are able to reduce the carbon footprint of your devices because no additional FR4 board is required for the glass.
Individual design
Timeless aesthetics, the incomparable feel of an elegant material from the front and printed electronics on glass with a powerful embedded controller on the back. These are our functionalized glass surfaces, which can be used excellently as input systems in almost all industries. With our IMPAtouch technology, we create the right user interface according to your individual requirements.
The ready-to-install assembly
With our know-how and the wide range of manufacturing options, we develop a ready-to-install assembly solution tailored to your product with cover frames, lighting, ESD protection, mounting options, adhesive points, sealing... We produce a ready-to-install assembly from many individual parts, saving you material, assembly and process costs. We reduce sources of error, shorten delivery times and minimize risks in the supply chain.